ANAGAMA Matcha Bowls - Eizan Kiln |
 |
- Manufacturing Process - Unloading ANAGAMA Pottery and Finishing |
|
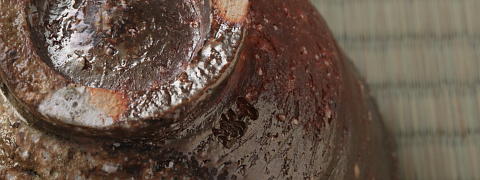 |
Main Topic |
 |
Seasonal Topics & Items |
 |
 |
Dear Sir and Madam, |
 |
We at Hibiki-an THANK YOU VERY MUCH for your continued patronage and support.
We are pleased to offer useful information for your healthy life and continued
enjoyment of Japanese green tea. In this issue, we talk about 'ANAGAMA Matcha Bowls - Eizan Kiln (Manufacturing Process - Unloading ANAGAMA Pottery and Finishing)'. |
 |
 |
ANAGAMA Matcha Bowls: One-of-a-kind piece / Now Available |
 |
We have begun to sell very special Matcha Bowls fired in the most traditional kiln, ANAGAMA by the ceramic artist Mr. Eizan Okuda.
ANAGAMA is an ancestor of the climbing kiln, a traditional style of kiln built on an upward incline. There is never one ANAGAMA the same as any other. Each work is one of a kind.(So, once sold, it will be out of stock.) ANAGAMA pottery is the art of the combination of earth and fire. It fascinates the artisan and touches the heart. Last autumn, Mr. Eizan produced some very beautiful and unique pieces of ANAGAMA pottery. The kiln firing continued from September 7th to 10th.
We, at Hibiki-an, are fortunate to be able to offer some of his ANAGAMA pottery. Please take a look. You are sure to fall in love. |
 |
 |
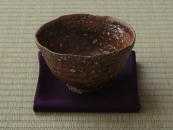 |
 |
[ANAGAMA Matcha Bowl] HOHJYOH-no-DAICHI (by Eizan Okuda): US$2,680.00
(One-of-a-kind piece / Now Available) HOHJYOH means fertile, when the land is fertile and crops grow well. DAICHI of this name means the earth in Japanese. HOHJYOH no DAICHI refers to the generosity and strength of the earth which gives us a bountiful harvest. A special clay created by Mr. Eizan Okuda was used to produce this dark brown Matcha bowl... |
 |
 |
 |
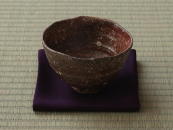 |
 |
[ANAGAMA Matcha Bowl] MINORI-no-UTAGE (by Eizan Okuda): US$2,080.00
(One-of-a-kind piece / Now Available) MINORI means crop or harvest and UTAGE means celebration in Japanese. The name evokes a lively celebration where people gather to welcome the bountiful harvest from the earth in autumn. This Matcha bowl was made using a hand-building technique. First Mr. Eizan Okuda makes coils and places them around the edge of the base in spirals... |
 |
 |
 |
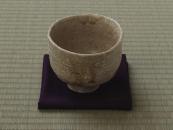 |
 |
[ANAGAMA Matcha Bowl] KANSETSU (by Hozan Tanii): US$2,080.00
(One-of-a-kind piece / Now Available) KANSETSU means snowcap. This Matcha bowl looks like a snowcapped mountain reflecting the sunlight. A thin covering of natural ash glaze created this beautiful white color during firing in the kiln. This KANSETSU Matcha bowl evokes the snowcapped mountain which towers with its majestic nobility... |
 |
 |
 |
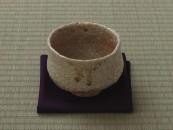 |
 |
[ANAGAMA Matcha Bowl] SOHSYUN (by Hozan Tanii): US$2080.00
(One-of-a-kind piece / Now Available) SOHSYUN means beginning of spring. The green gold color of BEEDORO glaze looks like new sprouts just starting to grow. The white color of this Matcha bowl looks like snow on the ground. A thin covering of natural ash glaze created this beautiful white color during firing in the kiln... |
 |
 |
 |
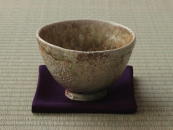 |
 |
[ANAGAMA Matcha Bowl] KUSANO-SHIRATSUYU (by Eizan Okuda): US$3,280.00
(Sold / Not Available) KUSA means grass, and SHIRATSUYU means white dew in Japanese, but it also refers to a day on the calendar, September 10th. This bowl was unloaded from the kiln on September 10th. This Matcha bowl has many fine aspects, such as its BEEDORO glaze, white and greenish brown spots, gradation color of HIIRO, and so on... |
 |
 |
 |
ANAGAMA Matcha Bowls - Eizan Kiln page: click here |
 |
 |
 |
ANAGAMA Manufacturing Process - Kiln Preparation, Placement of Works inside the Kiln
|
 |
ANAGAMA pottery is usually fired continuously for 4 days (96 hours) or more, using approximately 400 batches of firewood. Each batch has around 20 logs of firewood made from acicular trees. Japanese red pine makes a good natural glaze, however all bark must be removed because ash from bark does not create good glaze. It is not a simple task to prepare firewood for the kiln.
One of the most important steps before firing the kiln, is the arrangement or placement of the pottery inside the kiln. This is a trade secret of each artisan. The color and pattern of each ANAGAMA ceramic is created by fire in the ANAGAMA kiln and completely depends on where it is placed in relation to the flames. Each work is carefully placed, considering the path and direction of the fire in the kiln. The artisan positions the ceramics in the kiln, using his knowledge of how the flame will affect the color and pattern, and depending on how he wants the work to evolve.
Placement also affects the shape of each work. For example, if a Matcha bowl is set up sideways in the kiln, it naturally flattens when it is fired and the top face becomes a natural oval. When the Matcha bowl is placed sideways in the kiln, the fire makes contact with the inside of the Matcha bowl. So, the scene inside of the Matcha bowl becomes quite unique and excellent.
Shells are often used to add patterns on the works or adjust the burnt color. Shells are calcareous, containing high levels of calcium carbonate, so that they react to fire and create beautiful and intense color. Clam, abalone, and scallop are used as the situation demands.
As above, placement of each piece of pottery is one of the most important steps before firing the kiln. During placement, artisans carefully consider the color and pattern of the finished works. It is not unusual for the artisan to change and rearrange the position of the works several times before firing the kiln.
|
 |
 |
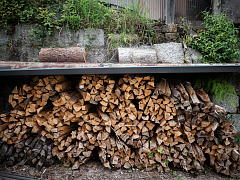 |
 |
Batches of firewood. This is just part of the 400 batches of firewood which are burned for 4 days (96 hours) or more continuously without break. |
|
 |
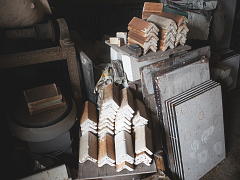 |
 |
Fireproof stones are used not only to hold the bowl in place during firing, but to add patterns to the work or to adjust the burnt color. |
|
 |
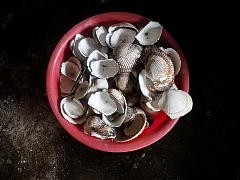 |
 |
The inside of the kiln is very small and the work is hard for the potterShells used for adding patterns or adjusting the burned color. To add patterns, works are placed on the shells. |
|
 |
 |
 |
 |
 |
The inside of the kiln is very small and the work is hard for the potterThe inside of the kiln is very small and the work is hard for the artisan. |
|
 |
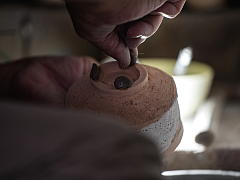 |
 |
Fireproof stones are used not only to hold the bowl in place during firing, but to add patterns to the work or to adjust the burnt color. |
|
 |
|
 |
 |
 |
|
 |
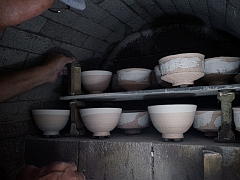 |
 |
All the potteries are set. All of them are arranged based on his vision. |
|
 |
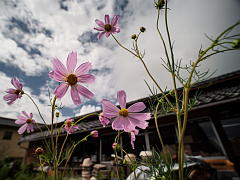 |
 |
Gradually, autumn is in the air. |
|
 |
 |
Matcha Bowls / Accessories shopping category: click here |
ANAGAMA Matcha Bowls - Eizan Kiln page: click here |
 |
 |
 |
ANAGAMA Manufacturing Process - Firing the Kiln
|
 |
ANAGAMA pottery is usually fired for 4 days (96 hours) or more continuously without break. Firewood is carefully placed in the kiln every 5 minutes. The burning temperature starts at 2,190F (1,200C) and peaks at 2,370F (1,300C) on the third or fourth day. The flame of the kiln is managed by Mr. Eizan Okuda and his assistants in turn, every six hours. During the four days of firing, the artisan can hardly sleep due to anticipation and the arduous process.
The artisan is able to precisely gauge and adjust the temperature in the kiln by watching the color of the smoke and changing the way of closing the mouth of the kiln and lid of the chimney. He can gauge the temperature in the kiln by the kinds of smoke coming out from the chimney. When black smoke emerges, the temperature is relatively low. Gray smoke means the temperature is in the middle range, while transparent smoke means the kiln is very hot.
The kiln can be closed using bricks, firewood, and an iron lid. If the iron lid is used, very little air can enter the kiln and the temperature does not rise. If bricks or firewood are used, air can easily enter the kiln, and the amount of air also can be precisely controlled.
In order to create the intended color and pattern, the artisan adjusts the conditions inside the ANAGAMA kiln, using an iron rod. It is not an easy task to change the position of works, using an iron rod through the small mouth of the kiln, which is only 11.8in x 11.8in (30cm x 30cm). It is also important work to control the flow of flames and ashes in the kiln.
At the last stage, on the third or fourth day, when the temperature in the kiln peaks at 2,370F (1,300C), a pillar of fire bursts forth from the chimney with an amazing sound. The scene is awesome and dramatic.
Mr. Eizan Okuda built his own ANAGAMA kiln in the traditional style with a steep incline and low ceiling. Fire can quickly and fully race around inside his ANAGAMA kiln, because of the strong air flow that can more easily enter the kiln by the steep incline and low ceiling. So, the unique and excellent color and pattern can be created. However, his style of ANAGAMA kiln requires highly skilled precision and enormous effort. Adjusting the temperature in the kiln is especially difficult. If the artisan loses his concentration even for a moment during the kiln firing, all of his works would be ruined.
|
 |
 |
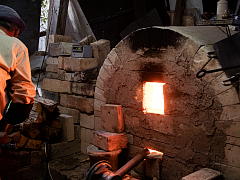 |
 |
Firing the kiln has just started. |
|
 |
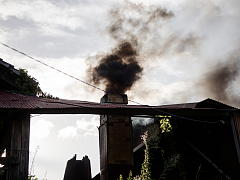 |
 |
Gray smoke emerging from the chimney |
|
 |
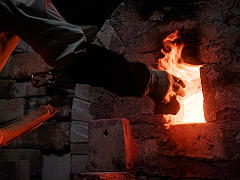 |
 |
Putting woods on a fire |
|
 |
 |
 |
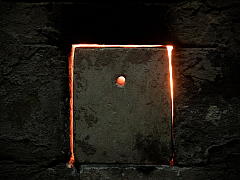 |
 |
The kiln mouth is closed with a thick stone lid. |
|
 |
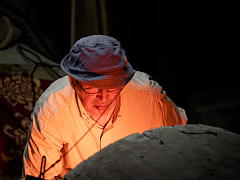 |
 |
In order to create the intended color and pattern, the artisan adjusts the conditions inside the ANAGAMA kiln, using an iron rod. |
|
 |
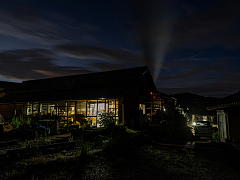 |
 |
It's slowly getting darker around the ANAGAMA kiln. |
|
 |
 |
 |
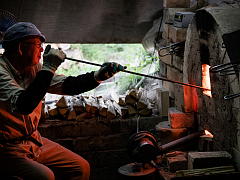 |
 |
Controlling the flames and ashes requires a high level of skill. |
|
 |
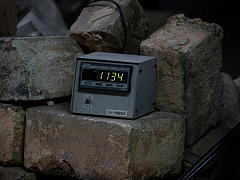 |
 |
A thermometer is used to confirm the temperature. |
|
 |
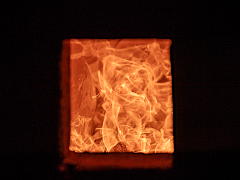 |
 |
Fire is quickly racing around inside the kiln. The scene is very dynamic and completely captivating to anyone who sees it firsthand. |
|
 |
 |
 |
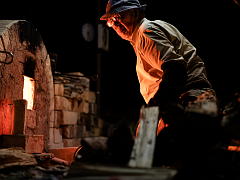 |
 |
He has very earnest eyes for his dearest potteries. |
|
 |
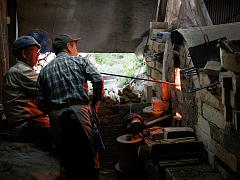 |
 |
He works with the staff to manage the kiln. |
|
 |
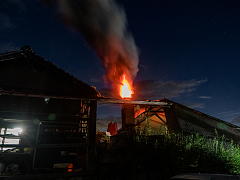 |
 |
A pillar of fire bursts forth from the chimney in the silent night. The scene is dramatic. |
|
 |
 |
Matcha Bowls / Accessories shopping category: click here |
ANAGAMA Matcha Bowls - Eizan Kiln page: click here |
 |
|